Petroleum Refining - Compressor |
Case Study # 111 |
Although the equipment particle
concentration (EPC) of 3,046 is well within the historic mean for this
equipment, analysis of equipment particle size, shape and
composition indicate spalling of the babbitt material, from Refinery
NTSG compressor. The equipment was rated
CRITICAL. Recommendation:
Schedule equipment for maintenance action.
Inspection for abnormal bearing wear mode in progress and damage to
journal (sleeve) bearing. |
 |
|
|
Equipment Particle Analysis
(EPA) shows 130 micrometer (um) white non-ferrous (Babbitting Alloy)
Severe Sliding Wear particles. Analysis also shows the presence
of 55um Copper Alloy (including Brass & Bronze) Severe Sliding wear
particles. These particle are of sufficient size to cause
a metal to metal interference with the close tolerances of this film
boundary lubrication of this equipment.
Heat treatment of these 130um white non-ferrous metal particles
confirm their composition of babbitting alloy. Evidence from the
equipment particle profile indicate pitting and spalling of the
babbitt layer of the sleeve or journal bearing. |

 |
|
|
Upon opening of NTSG
Compressor,
three-(3) of the five-(5) sets of sleeve or journal bearings show
pitting and spalling. Significant secondary damage was avoided
resulting in the saving of the crankshaft in this reciprocating
compressor. |
 |
CUSTOMER ESTIMATED
COST SAVINGS: Original Component
Savings: 210,000
Secondary Damage Savings:
72,000
Down Time Min./Production hrs. Savings:
0
RUSH Shipping Cost Savings:
0
Parts & Inventory Warehouse Savings:
0
Overtime Repair Savings: 0
Total SAVINGS:
$ 282,000 |
|
 |
Making your PM Program mean .... "Profit Making"ä
Experience Since 1985 |
800.483.R7E3A2L5 |
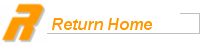 |
 |