Equipment Particle
Analysis is often confuses with Oil Analysis.
However, ferrography uses precision magnets to strip iron-laden and other
susceptible particles from a used lube oil for study; results indicate
extent of equipment wear and likelihood of imminent failure.
Direct-Reading Ferrography uses optical sensors to measure the density
of particles collected and the ratio of large particles to small
(fatigue-related catastrophic failure generally is characterized by
generation of particles larger than 10-15 microns or um).
The DR obtains two-(2) sets of readings:
first for Direct Large (DL) >5um and the second for Direct Small
(DS) ≤5um
particles. The Wear Particle Concentration (WPC) is calculated by adding DL
+ DS = WPC divided by the volume of sample, establishing a
machine wear trend baseline. Other helpful particle calculations include:
Wear Particle Concetration
|
(WPC) |
DL + DS
= WPC |
Percentage Large Particles
|
(PLP) |
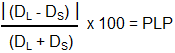 |
Wear Severity Index |
(WSI) |
(DL + DS) (DL
- DS) = WSI |
Analytical Ferrography employs photo and optical microscopic
techniques for evaluation of equipment particles. This evaluation involves
discriminating the particles by Size, Shape, Composition & Concentration and
relates these characteristics to the four-(4) known wear mechanisms or
Rolling, Sliding, Spinning and Impaction. The test provides in-depth
analysis of particle makeup discriminating metals from non-metal and ferrous
metals from non-ferrous metals (e.g., high carbon steel (~12%), case
hardened steel, cast iron, copper alloys, brass, bronze, aluminum, tin and
corrosion or oxides).