are a type of
air bearing also refered to as gas bearing or
fluid bearing. A shaft is supported by a compliant, spring loaded
foil journal lining. Once the shaft is spinning fast enough, the working
fluid
(usually air), pushes the foil away from the shaft so that there is then no
contact. The shaft and foil are separated by the air's high pressure which
is generated by the rotation which pulls gas into the bearing via viscosity
effects. A high speed of the shaft with respect to the foil is required to
initiate the air gap, and once this has been achieved, no wear occurs.
Whereas, aero or hydrostatic bearings, foil bearings require no external
pressurisation system for the working fluid, so the hydrodynamic bearing is
self-starting. Anti-wear coatings exist that allow over 100,000 start/stop
cycles for typical applications. New third generation bearings can hold 9000
times their weight, at extremely high speeds.
Turbomachinery is the most common application because foil bearings
operate at high speed.
Foil bearings were first developed in the late 1950s by
AiResearch Mfg. Co. of the Garrett Corp.
.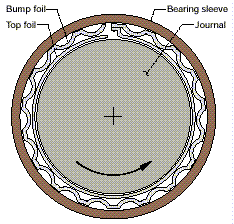
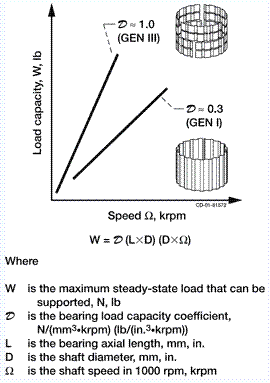
Also see fluid bearing.